Low-Cost Additive Manufacturing Technique for Metal Deposition on Delicate Substrates
A 1-step technique to deposit metals onto difficult substrates, enabling precise, high-adhesion, low-temp printing, ideal for electronics
Image credit: I Stock (guteksk7)
Background
Additive manufacturing, also known as 3D printing, has great potential to help realise the goals of industry 4.0 and 5.0. These goals include more adaptable, efficient, and environmentally friendly production processes.
Current metal additive manufacturing methods, such as ink-jet printing, typically use high temperatures, and/or complex processing steps. These approaches severely limit the ability to combine different materials as incompatible low-temperature materials like plastics or biologics, would degrade or become damaged during the printing process.
Electronics manufacturing is especially impacted by this limitation. Many modern electronic devices require flexible plastic substrates (such as those used in flexible screens or wearable devices) combined with metal circuitry for conductivity. Standard metal printing processes are unable to deliver a solution onto combinations of hard to bond, heat-sensitive surfaces and complex structures, restricting design and functionality options.
Traditional printed electronics also involves pre- and post-processing steps, adding cost, time, and complexity to manufacturing. Additionally, the solvent-based inks used are less sustainable, expensive and can compromise adhesion, meaning that printed metals may not stick well to certain surfaces. This limits the durability and reliability of the final products, especially in sectors like automotive and wearable electronics.
UCL researchers have developed a novel atmospheric plasma jet (APPJ) printing method that addresses these issues by enabling metal printing at low temperatures. This allows it to work with a wider range of materials, including plastics and biologics, and removes the need for solvents, complex processing steps, and multiple stages. The result is a faster, more adaptable, and environmentally friendly manufacturing option.
Technology Overview
UCL researchers have demonstrated that APPJ printing can be used to print a range of metals (silver, copper, nickel, zinc, cadmium, cerium and palladium) on delicate substrates.
Figure 1: Copper printed directly onto a leaf
Figure 2: Copper circuitry printed onto pig skin
Figure 3: Antenna printed onto Kapton
Conductivity and adhesion have been demonstrated to be on par or better than existing ink jet printing technology and significant reductions in cost are likely.
Benefits
This APPJ printing method provides a sustainable method of printing metals on a range of substrates at low temperatures. Other benefits include, ultra-high adhesion, low-cost solvent-free inks, low power consumption and no requirements for pre or post-processing.
“Choose the material you want to print on, not the material you can print on.”
• Low temperature – not limited to heat-resistant substrates allowing a wide range of plastics and biological materials
• High adhesion – improves bonding to difficult substrate such as Polyolefins, Kapton and ceramics – reducing QA/QC issues
• 1-step process –simpler and more cost-effective – combines cleaning, surface activation, printing in one-step, no post-processing required
• Unique control of chemistry – open to novel combinations and functional coatings, fine-tune to your requirements
Applications
The technology is applicable to all industries where the deposition of conductive metals are critical to manufacturing. These include but are not limited to:
Automotive manufacturing
• Printing conductive circuitry on flexible, low-temperature plastic parts for in-car electronics
• Direct metal deposition for lightweight sensors and connectors
Wearable devices
• Integrating flexible metal circuitry onto fabrics and plastic materials for smart textiles
• Low-temperature printing on skin-safe substrates for health monitoring patches
Energy industry
• Printing metallic electrodes for flexible batteries and capacitors
• Coating photovoltaic panels with metal layers to enhance conductivity and durability
Optics
• Depositing thin metal layers on optical components to improve light control
• Printing anti-reflective and conductive coatings for lenses and optical sensors
Nanotechnology
• Creating nano-scale metal patterns on sensitive substrates
• Fabricating metal-coated surfaces for drug delivery systems or sensor applications
Semiconductor industry
• Low-temperature metal deposition for flexible electronics and microchips
• Direct deposition of metal contacts onto heat-sensitive substrates in semiconductor manufacturing
Telecommunications
- Printing antennas on flexible substrates for mobile devices and IoT sensors.
Opportunity
UCLB is looking for commercial partners to explore bringing this technology to market.
Seeking
• Development partner
• Commercial partner
• University spinout
• Seeking investment
IP Status
• Patented
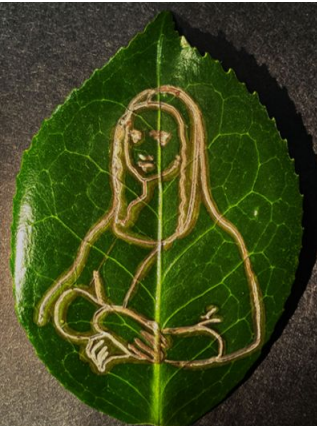
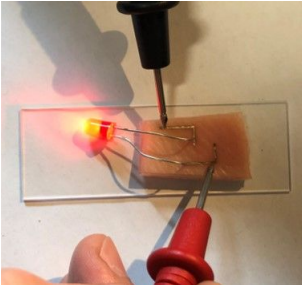
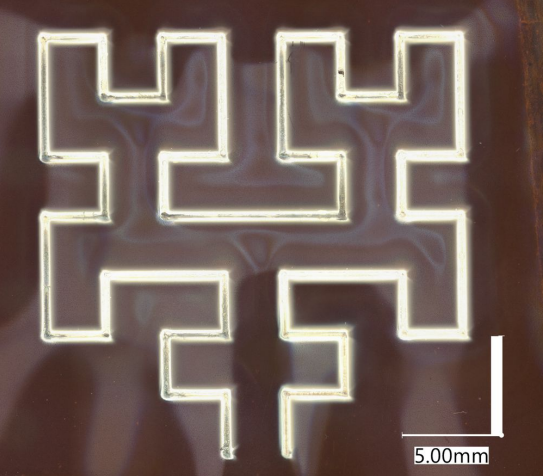